5-Axis Trunnion Assembly
A high-precision electromechanical fixture enabling 3+2 and full 5-axis CNC machining.
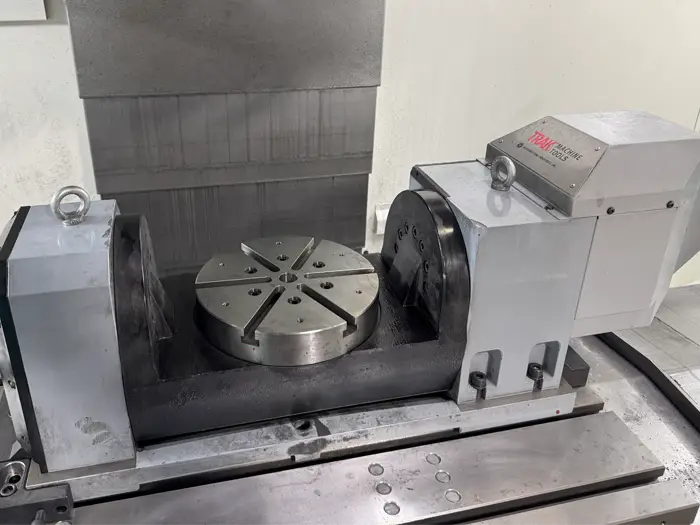
As an example of the complex, high-performance subsystems we produce, SWI Systems manufactured a precision trunnion table for integration into a new 5-axis CNC platform. This electromechanical fixture was built entirely in-house for TRAK Machine Tools and is designed to enable both 3+2 and full 5-axis machining. It reflects our ability to build sophisticated assemblies that combine tight-tolerance machining, advanced motion control, and long-life reliability—hallmarks of our contract manufacturing capability.
The trunnion's compact, low-profile build—just 8 inches from the mill table to the platter—sets it apart from comparable systems, which typically stand 12 inches or taller. This shorter profile allows for increased Z-axis travel, expanding the usable machining envelope. Inside the unit is a complex mechanical structure that includes a robust tilt mechanism capable of +/-130 degrees of motion—exceeding typical ranges and providing greater part access and tool reach.
Project Details
- 3+2 and 5th-axis Trunnion
- Designed and manufactured in house
- More tilt than competitors: +/- 130 degrees
- 25% more torque than competitors
- Lower profile than competitors
- Cycloidal type reducers outperforms worm drives
- Maintenance-free and lifetime lubrication
To support demanding machining conditions, the system delivers over 350 ft-lbs of continuous torque and up to 1000 ft-lbs peak. It is sealed and lubricated for life, providing a true maintenance-free experience. The entire assembly was built to rigid mechanical and quality standards, drawing on SWI Systems' strengths in mechanical precision, drive integration, and electromechanical subassembly.
At the core of the trunnion's durability is its cycloidal drive system—an advanced reducer design we've successfully deployed in other TRAK products for more than a decade. This “rolling” motion drive eliminates backlash, avoids wear, and maintains strength over time. The successful implementation of this system once again demonstrates our ability to deliver motion-enabled assemblies with proven reliability for OEM platforms or high-spec industrial applications.